Introduction to Home Paint and Texture Manufacturing
The home paint and texture manufacturing industry holds a pivotal role in modern home decor and construction. Paints and textures are essential not only for enhancing the aesthetic appeal of living spaces but also for providing protective coatings for building surfaces. Over the years, the industry has evolved significantly, leveraging advancements in technology and materials to meet the ever-growing demand for high-quality and durable products.
In the realm of home decor, the importance of paint cannot be overstated. Paint defines the character and ambiance of a home, offering a spectrum of styles from vibrant and bold to subtle and serene. Similarly, textured finishes add depth and dimension to walls and ceilings, allowing homeowners to express their unique tastes and preferences. The correct combination of colors and textures can transform a simple room into an inviting, visually appealing space.
More than just a style element, home paint serves a functional purpose by acting as a protective barrier for surfaces. These coatings shield homes from environmental factors like moisture, ultraviolet rays, and pollutants, which can cause wear and degradation over time. Recent advancements have also focused on eco-friendly formulations, promoting sustainability without compromising on performance and aesthetic quality.
The history of paint manufacturing dates back thousands of years, with early civilizations utilizing natural pigments from minerals, plants, and clays. As time progressed, the processes became more sophisticated, incorporating chemical innovations and industrial methods. The industrial revolution marked a significant turn, with the introduction of mass production techniques, synthetic pigments, and advanced mixing processes, leading to consistent quality and wider availability.
Today, the home paint and texture manufacturing industry is a complex and highly specialized field, balancing tradition with modern innovation. Manufacturers continually research and develop new materials and techniques to provide products that not only fulfill aesthetic desires but also meet stringent environmental and safety standards. This synergy of art, science, and technology underscores the continued relevance and evolution of the industry in enriching and protecting our living spaces.
Raw Materials Used in Paint Manufacturing
The manufacturing of home paint involves a meticulous selection of raw materials, each playing a crucial role in imparting the desired characteristics to the final product. One of the fundamental components is the pigment, responsible for providing the color and opacity of the paint. Pigments can be either organic, derived from carbon compounds, or inorganic, synthesized from minerals. Popular inorganic pigments include titanium dioxide for white paint and iron oxides for earthy tones such as reds, browns, and yellows.
Binders, also known as resins, are another essential ingredient. These substances hold the pigment particles together and ensure they adhere properly to the painted surface. Common binders in home paint manufacturing include acrylic, alkyd, and epoxy resins, each contributing unique properties such as flexibility, durability, and resistance to environmental factors. The choice of binder largely dictates the quality and performance of the finished paint product.
Solvents play a critical role as well, primarily serving to dissolve the binders and create a uniform mixture. Solvents such as water in latex paints or mineral spirits in oil-based paints facilitate the application process by adjusting the paint’s viscosity. As the paint dries, the solvent evaporates, leaving behind a solid, durable film of paint. Given growing environmental concerns, manufacturers are increasingly developing low-VOC (volatile organic compounds) solvent alternatives to reduce harmful emissions.
Lastly, additives are incorporated to enhance specific attributes of the paint. These can include anti-foaming agents, stabilizers, and UV protectors. Anti-foaming agents prevent the formation of bubbles, stabilizers ensure the dispersion of pigments and binders is homogenous, and UV protectors help the paint resist degradation from sunlight exposure, thereby extending its longevity.
The sourcing and quality of these raw materials play a pivotal role in the home paint manufacturing process. Manufacturers often seek reputable suppliers who can consistently provide high-quality pigments, binders, solvents, and additives. The chemical properties of each component are meticulously analyzed to ensure they meet industry standards, thereby guaranteeing that the final product will deliver superior performance in consumer applications.
The Manufacturing Process of Paints
The journey from raw materials to the finished home paint involves a meticulous series of steps designed to ensure quality and consistency. The process begins with the initial formulation, where chemists develop a precise recipe that combines pigments, solvents, resins, and various additives. Each component is carefully measured to achieve the desired color, texture, and durability of the paint.
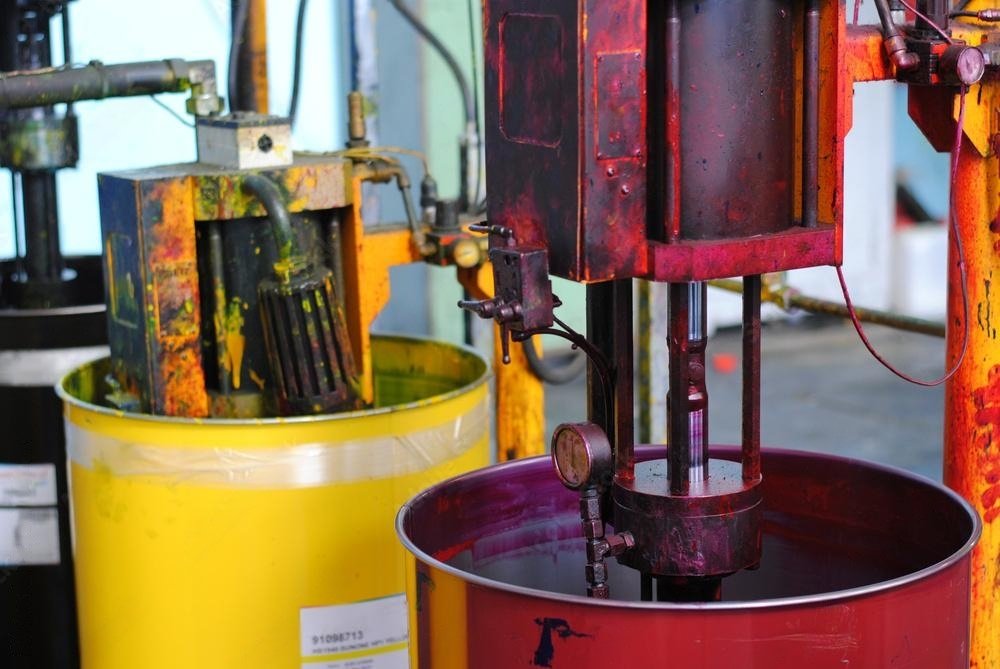
Once the formulation is established, the raw materials are then mixed together in large vats. This stage, known as premixing, involves combining the dry pigments with the resins and solvents. High-speed mixers are used to create a uniform mixture, ensuring that the pigments are thoroughly wet out by the resin and solvent, which is crucial for producing a smooth and even home paint.
The next stage is grinding, where the premixed batch is processed through large mills to break down agglomerates and achieve finer particle sizes. This enhances the color strength and gloss of the paint. Following grinding, the mixture undergoes dispersion, which involves further breaking down the pigment particles and ensuring they are evenly distributed throughout the medium. This stage typically utilizes high-speed dispersers or sand mills to achieve the optimal dispersion state.
After dispersion, the letdown stage occurs. This phase involves diluting the concentrated pigment paste with additional solvents, resins, and other additives to achieve the final product consistency. The paint is constantly monitored and adjusted to ensure it meets the desired viscosity, flow, and application properties.
Throughout each of these stages, quality control measures are diligently implemented. Samples are taken at various points to test for parameters such as color accuracy, drying time, and overall performance. These tests ensure that the home paint produced not only meets industry standards but also satisfies the varying needs of consumers.
By adhering to these rigorous steps and quality checks, manufacturers can consistently produce reliable and high-quality home paints that perform well under different conditions and offer lasting aesthetic appeal.
Types of Home Paints and Their Applications
When discussing home paint, it’s essential to recognize the variety of types available to suit different surfaces and environments. Each type of paint has unique properties that make it suitable for specific applications. Let’s explore four primary categories: interior paint, exterior paint, enamel paint, and latex paint.
Interior Paint: As the name suggests, interior paint is designed for application inside buildings. It emphasizes ease of cleaning and resistance to staining. Typically, these paints have a lower level of volatile organic compounds (VOCs), ensuring minimal odor and better air quality within living spaces. Interior paint comes in various finishes such as matte, eggshell, satin, and semi-gloss. Each finish offers a different look and functionality, making them versatile for walls, ceilings, and furniture.
Exterior Paint: Exterior paints are formulated to withstand harsh weather conditions, including UV radiation, rain, and temperature fluctuations. They are more durable than interior paints, offering protection against peeling, blistering, and fading. Exterior paints often include fungicides and algaecides to prevent mold and mildew growth. Suitable surfaces for exterior paint include wood, brick, concrete, and metal, ensuring the structural and aesthetic longevity of façades.
Enamel Paint: Known for its hard, glossy finish, enamel paint is extensively used in areas that require a durable and washable surface. This type of paint is suitable for woodwork, trim, doors, and kitchen cabinets. It provides an excellent protective layer, making it resistant to scratches and stains. Enamel paint can be used both indoors and outdoors, though it is especially favored for high-traffic areas and surfaces with frequent contact.
Latex Paint: Water-based latex paint is popular due to its ease of application, quick drying time, and minimal odor. It is available in various sheens and can be used for both interior and exterior projects. Latex paint is eco-friendly and easy to clean up with soap and water, making it a practical choice for most home painting needs. It adheres well to a variety of surfaces, including drywall, plaster, and wood, providing a flexible and durable finish.
Understanding the types of paints and their specific applications is critical for making informed decisions regarding home improvement projects. Selecting the right paint ensures both the aesthetic appeal and longevity of painted surfaces.
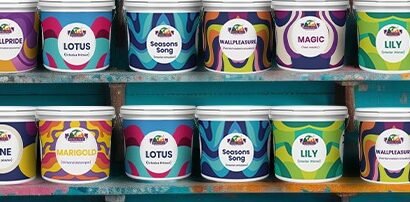
Texture Manufacturing and Applications
The manufacturing of wall textures is a meticulous process that combines the right materials and equipment to achieve an array of aesthetically pleasing and functional outcomes. Various textures such as knockdown, orange peel, and popcorn each serve distinct purposes and provide different visual effects, enhancing the overall appeal of home interiors.
The primary materials involved in texture manufacturing often include joint compounds, plaster, and specialized additives that promote the desired texture qualities. Joint compound, commonly used for knockdown textures, provides a versatile base that can be easily manipulated with tools after application. Orange peel and popcorn textures frequently utilize a mix of compound and aggregates like polystyrene or vermiculite to generate their unique appearances.
Equipment plays a critical role in the application process. For orange peel and knockdown textures, a spray gun attached to an air compressor is typically employed. This equipment enables uniform distribution of the compound over the wall surface. Conversely, popcorn texture application often requires a larger hopper gun to accommodate the heavier consistency of the mixture.
Each texture type entails its own specific techniques for optimal application. The knockdown texture, for instance, is first sprayed onto the wall, then flattened slightly with a wide knife, creating a smooth but visually interesting finish. Orange peel, true to its name, is sprayed to mimic the dimpled texture of citrus skin, providing a subtle, refined look. Popcorn texture, predominantly used on ceilings, is sprayed to form a heavier, more pronounced finish that effectively hides imperfections.
Textured finishes not only enhance the aesthetic value of a space but also offer several functional benefits. These finishes can mask surface imperfections, thereby reducing the need for extensive wall repairs. They also add depth and dimension to a room, influencing light and shadow to create a dynamic environment. Additionally, certain textures can improve acoustics by minimizing sound reflection, contributing to a quieter home setting.
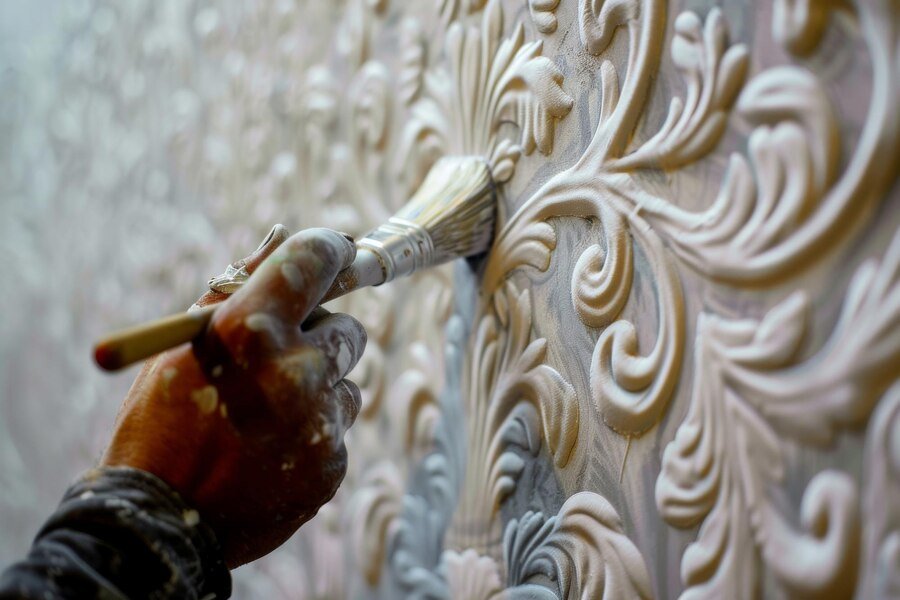
In summary, the art and science of texture manufacturing in home paint provide diverse opportunities for creativity while offering practical advantages. Whether aiming for a subtle elegance or a bold statement, textured finishes enable homeowners to achieve their design aspirations.
Innovations and Trends in Paint and Texture Manufacturing
The home paint and texture manufacturing industry has witnessed significant advancements, responding to evolving consumer preferences and increased environmental awareness. One of the most notable trends is the growing demand for environmentally friendly and sustainable products. Manufacturers are now focusing on developing paints with reduced volatile organic compounds (VOCs), ensuring fewer hazardous emissions and a healthier indoor environment. This emphasis on sustainability extends to sourcing raw materials responsibly and adopting greener manufacturing practices.
Alongside sustainability, technological advancements play a crucial role in modernizing the industry. Innovations in formulation have led to the creation of high-performance home paints that are more durable and easier to apply. For instance, nanotechnology is being utilized to create self-cleaning and anti-microbial surfaces, enhancing the lifespan and hygiene of painted surfaces. Additionally, smart coatings that change color with temperature fluctuations or light exposure are now available, adding a level of functionality and aesthetic appeal previously unattainable.
Moreover, digital technology is revolutionizing how consumers interact with home paint products. Augmented reality (AR) applications enable customers to visualize various paint colors and textures in their spaces before making a purchase, ensuring a personalized and satisfactory experience. This trend is complemented by the growing popularity of e-commerce platforms, making it easier for consumers to access a wide range of products and make informed choices from the comfort of their homes.
Finally, evolving consumer preferences are shaping the market landscape. The desire for unique and personalized aesthetics has led to an interest in custom textures and finishes. Whether it’s matte, satin, or high-gloss, consumers are experimenting with different textures to create bespoke home environments. This trend indicates a shift towards more individualized and expressive home decor choices, driving manufacturers to continually innovate and expand their product lines.
Quality Assurance and Testing in Paint Manufacturing
The rigorous quality assurance processes implemented in the paint manufacturing industry are indispensable in ensuring the performance and reliability of home paint products. These processes involve a series of stringent tests designed to evaluate various aspects of the paint’s properties, thereby guaranteeing its suitability for a wide range of applications.
One of the primary tests conducted is the adhesion test, which assesses the paint’s ability to adhere to different surfaces. This is crucial, as poor adhesion can lead to peeling, flaking, and a compromised finish. Techniques such as cross-hatch testing are employed to measure how well the paint bonds to various substrates, ensuring it remains intact over time.
Another vital component of quality assurance is the durability test. Durability encompasses the paint’s resilience against physical wear and tear, ensuring it can withstand everyday usage. This includes examining the paint’s resistance to scrubbing, washing, and general abrasion, which are critical for maintaining an impeccable appearance on walls and other surfaces.
Resistance to external factors is another key focus area. Weather resistance tests evaluate how well home paint holds up under extreme climatic conditions, including prolonged exposure to sunlight, humidity, and temperature fluctuations. Similarly, chemical resistance tests determine the paint’s ability to resist stains, solvents, and other chemical agents, which is particularly important for applications in industrial or high-use areas.
Color consistency is equally critical, as it ensures that the paint maintains uniformity across different batches. Manufacturers employ meticulous color matching techniques, using spectrophotometers to measure and compare colors, ensuring an exact match to the desired hue and shade. This not only upholds aesthetic standards but also enhances customer satisfaction.
To align with industry norms, paint manufacturers must comply with established standards and certifications. Organizations such as the American Society for Testing and Materials (ASTM) and International Organization for Standardization (ISO) set benchmarks for various quality parameters. Adherence to these standards is indicative of a manufacturer’s commitment to delivering high-quality home paint products.
Through comprehensive testing and adherence to stringent industry standards, paint manufacturers ensure their products provide enduring protection, aesthetic appeal, and satisfaction to the end user.
Conclusion: The Future of Home Paint and Texture Manufacturing
The evolution of home paint and texture manufacturing has consistently marched towards enhancing quality and sustainability. As we have journeyed from discussing the raw material selection to the intricate processes of formulation and production, the common thread has been the industry’s focus on innovation. The future promises even more transformational changes, driven by rapid technological advancements.
One of the pivotal drivers of future growth will undoubtedly be the integration of cutting-edge technologies. Smart paint, incorporating functionalities such as high energy efficiency, self-cleaning properties, and even pollution reduction, is set to redefine industry standards. Digitalization of manufacturing processes, through automation and AI, will streamline production, increase precision, and reduce waste, further amplifying sustainability efforts.
Regulatory changes will also play a crucial role in shaping the landscape of home paint manufacturing. Stricter environmental regulations and the push for non-toxic, eco-friendly materials will continue to gain momentum. Manufacturers must adapt by investing in research and development to formulate safer, greener alternatives without compromising on performance or durability.
Market demand is shifting too, as consumers become more environmentally conscious and demand products aligning with sustainable principles. This shift offers manufacturers an opportunity to differentiate themselves by emphasizing unique texture finishes and environmentally responsible practices. Embracing this trend will not only meet customer expectations but also serve as a competitive edge in a crowded market.
In a future where innovation and sustainability are paramount, the industry must not only keep pace with changes but also anticipate and lead them. By integrating new technologies, adhering to evolving regulations, and responding to market demands, home paint and texture manufacturers can thrive and contribute positively to environmental stewardship. The journey of home paint is far from over; indeed, it is on the cusp of an exciting, transformative era.